HYDRAULIC ACTUATOR :
- Suhel Patel
- Apr 30, 2020
- 2 min read
We already have discussed pneumatic actuator in my past article, Today I will cover the second type of actuator and where it used mostly?
A hydraulic actuator as the name indicates it used liquid pressure to move the valve mechanism.
It follows the principle of the pascal, it states that pressure applied to a confined fluid at any point is transmitted equally throughout the fluid in all direction.
F = PA (F = force, P = pressure, A = Area)
Almost in every hydraulic type of actuator piston is used rather than diaphragm to convert fluid pressure into mechanical force.
Where it requires very high pressure to operate valve mechanism hydraulic actuator is used.
To overcome friction in piston type hydraulic actuator lubricating nature of hydraulic oil is enough as oil serves as both to provide force and reduce friction by applying lubrication at the same time.
With modest and very less piston area using piston type of hydraulic actuator capable of produce tremendous amount of the actuating force.
If hydraulic [pressure of 2000 PSI applied on 3" diameter piston it will produce force over 14000 pounds and that is huge!
In addition to producing a high amount of the force using hydraulic oil, they also provide accurate positioning due to non-compressibility of the hydraulic oil.
If the passage from hydraulic oil to the cylinder is blocked by some valve, the actuator will remain in the same position, this is an advantage of such actuator where it can resist forces generated on the valve by the process fluid.
Hydraulic actuator contains their own electrically controlled pump to provide hydraulic fluid power, so the valve is actually controlled by the electrical means.
Other hydraulic actuators use a separate fluid power system to provide force to operate the valve.
With little advantage of this type of actuator, there is also some disadvantage it contains.
1. Thick large tubing is required.
2. Chances of a leak due to a large network.
3. Lack of intrinsic power storage.
4. Need to purge the system.
5. Environment influences like temperature change.
6. Limited acceleration.
In 3rd point lack of intrinsic power, storage means in comparison with pneumatic actuator due to its property of compressibility we can store extra air in a pressurised tank in case of air failure, whereas in hydraulic it is not possible.
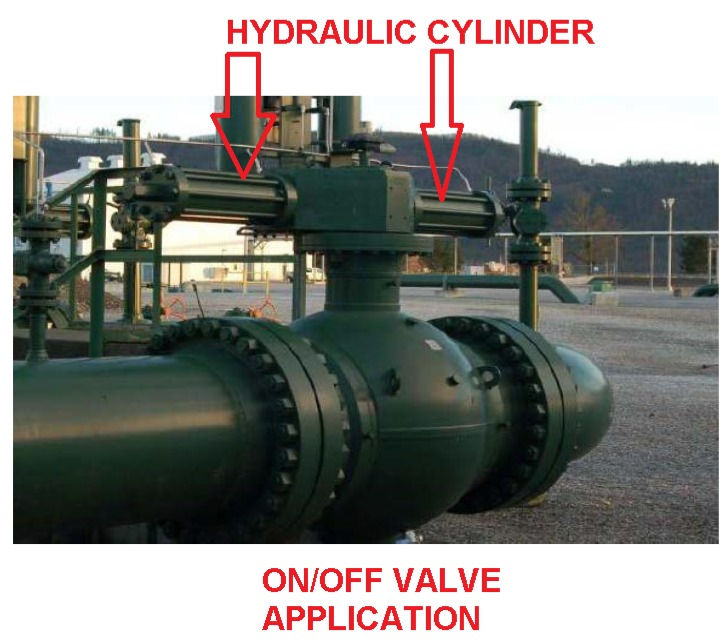
Here in the picture, you can see an application of hydraulic type actuator used for on/off actuation use two hydraulic cylinders contain rack and pinion assembly to convert linear motion to rotary motion.
Here is the same case as the pneumatic actuator to understand single acting and double acting.
In single-acting fluid pressure only applied on a single side of a piston, return stroke is given by spring.
In double-acting fluid pressure acts on both side of piston because it won't contain spring for the return stroke.
Comments