DEFINITION OF P, I, D TERM USED IN PID CONTROLLER :
- Suhel Patel
- Nov 19, 2020
- 3 min read
Updated: Nov 22, 2020
In this article, we will learn a term P, I, D used in the PID controller equation.
Before going through separate PID, let understand the definition of PID in brief. we will learn the PID controller with a practical example in a future lesson.
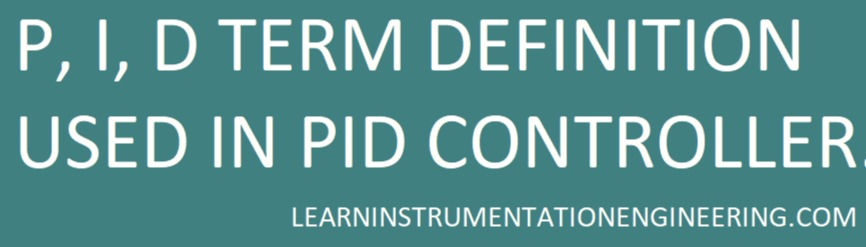
WHAT IS PID?
PID is a controller which can be board mounted or PID which come within PLC programming software.
You may have seen many onboard types of PID in which they do not require PLC programming to keep set point at a process variable.
PID stands for proportional, integral and derivative is an algorithm which is used to keep set point at process variable by using the final control element called control valve.
Let understand each term to ease your difficulty with the PID controller.
1) Proportional controller system
- In a proportional controlled system with proportional action, the process variable changes in proportional to the manipulated variable to keep the process at set point.
- Here, process variable follows the manipulated variable without any leg.
- When the time leg between the process variable and manipulated variable is too small then it does not have any effect on the system.
- For example in the flow control application, If valve travel changes in pressure control system then a new flow rate will reach instantaneously. In this case process variable changes proportional to the manipulated variable.
- Regardless of the other controlled action this proportional action always leave an offset which then solved by adding integral or derivative control action in it.
- Sometime proportional action called as gain. In the tuning process, we calculate gain to keep the process variable at a set point.
- Gain is given by the below equation,
Gain = change in process variable/change in the output
- For example, if a 20% change in output leads 10% change in the input then you will have a gain of 0.5
- When an error is large you can refer it to proportional action.
2) Integral control system
- This action will occur based on how long the error stays. so, longer the error more contribution integral action will give.
- In integral action, an error is integrated over a period of time until it reaches its set point.
- For example in a tank where the liquid is continuously supplied and discharging out, the tank level will fall and rise. so, the faster level changes the larger difference you will have in supply and discharge.
- In the tuning process we use the integral time to keep process variable at a set point. the smaller time has a larger impact and a larger time has a smaller impact.
- In my upcoming article, I will explain to you several parameters that affect an integral action like dead time, energy-storing component, etc.
- We sometimes called integral term as a reset.
- Proportion action acts on a present and integral action acts on a past.
- Integral action is the ration of the output velocity to the input error,
Integral action = Output velocity
Input error
3) Derivative control system.
- Derivative action also called a rate. Like proportional and integral action, derivative action reacts to how fast output will react based on changes in the process variable.
- Integral action react to the future.
- Derivative action can not be used in noisy processes. For example where flow rate needs to keep maintained at 2000 kg/hr. It fluctuating a lot like 1950, 1990, 2010, 2040 kg/hr. In such a condition you can use derivative action as it reacts fast can cause damage internal component of a control valve.
- A derivative action can be given by the following equation,
Derivative action = Output offset/ Input velocity
- The more changes you will make with derivative time the larger effect it will have.
This is a very basic explanation on three-term of the PID controller. Hope it will be helpful to you.
If you like this article then please do like and share among your friends.
Comentários