CONTROL VALVE POSITIONER :
- Suhel Patel
- May 4, 2020
- 2 min read
A control valve positioner is used to reduce friction and other mechanical influences, where it requires accurate control, where 3 to 15 psi pressure is not enough to operate a valve.
A positioner is an additional module which you have to link with a valve. first, air supply will come to positioner, from the positioner air is fed to actuator assembly based on the control signal.
Spring is used to convert mechanical force to motion for valve actuator, if a sole force acts on it it is okay to use without a positioner. But if any force acts upon the relation between applied pressure and valve stem will not be proportional.
But other forces also act on the valve-like friction from the stem packing, reaction force at valve plug due to differential pressure. To mitigate such issue valve positioner is used.
A valve positioner comes in three types with different operating principle.
- Force balance
- Motion balance
- Electronic positioner
I will cover each one in detail in my upcoming article. Let's only focus on positioner here.
A positioner is a motion- control device which actively compare valve stem position with the control signal. adjust the pressure and provide accurate control.
In this condition, it acts like a controller in which stem position is process variable (PV), Command signal to positioner is setpoint (SP) and positioner signal to control valve actuator is manipulated variable (MV).
Below is one the electronic type positioner of fisher widely used. But nowadays SMART positioner also used comes with an easy interface and allow us to do calibration within the display.
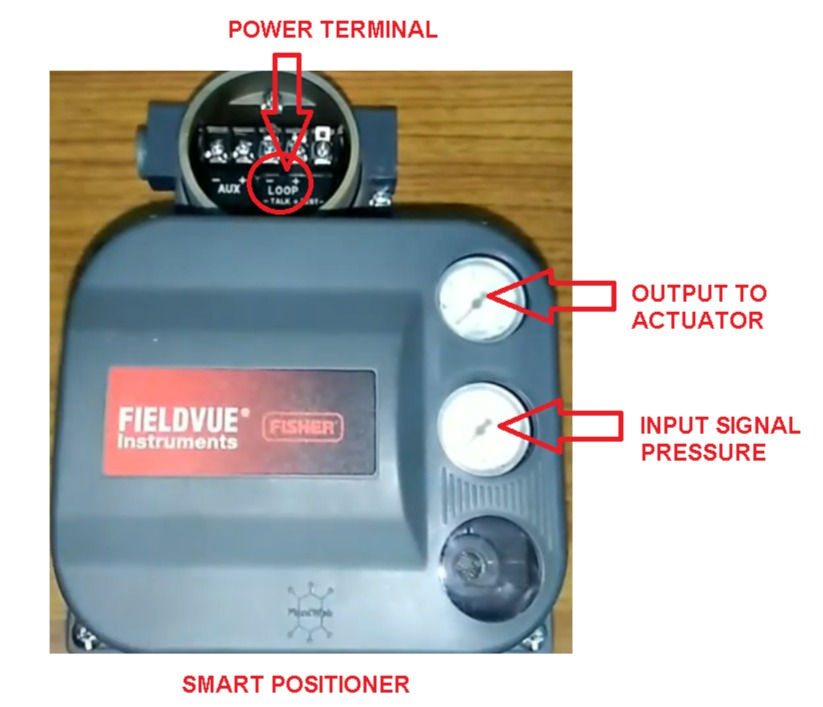
A positioner is designed in such a way that its source and vent air pressure faster, provide faster stem velocity thus reduce time delay. But in some condition like when air fails, it requires to use solenoid valve to vent pressure instantly.
Comments